Unlocking the Power of High Pressure Die Cast Tooling in Modern Metal Fabrication
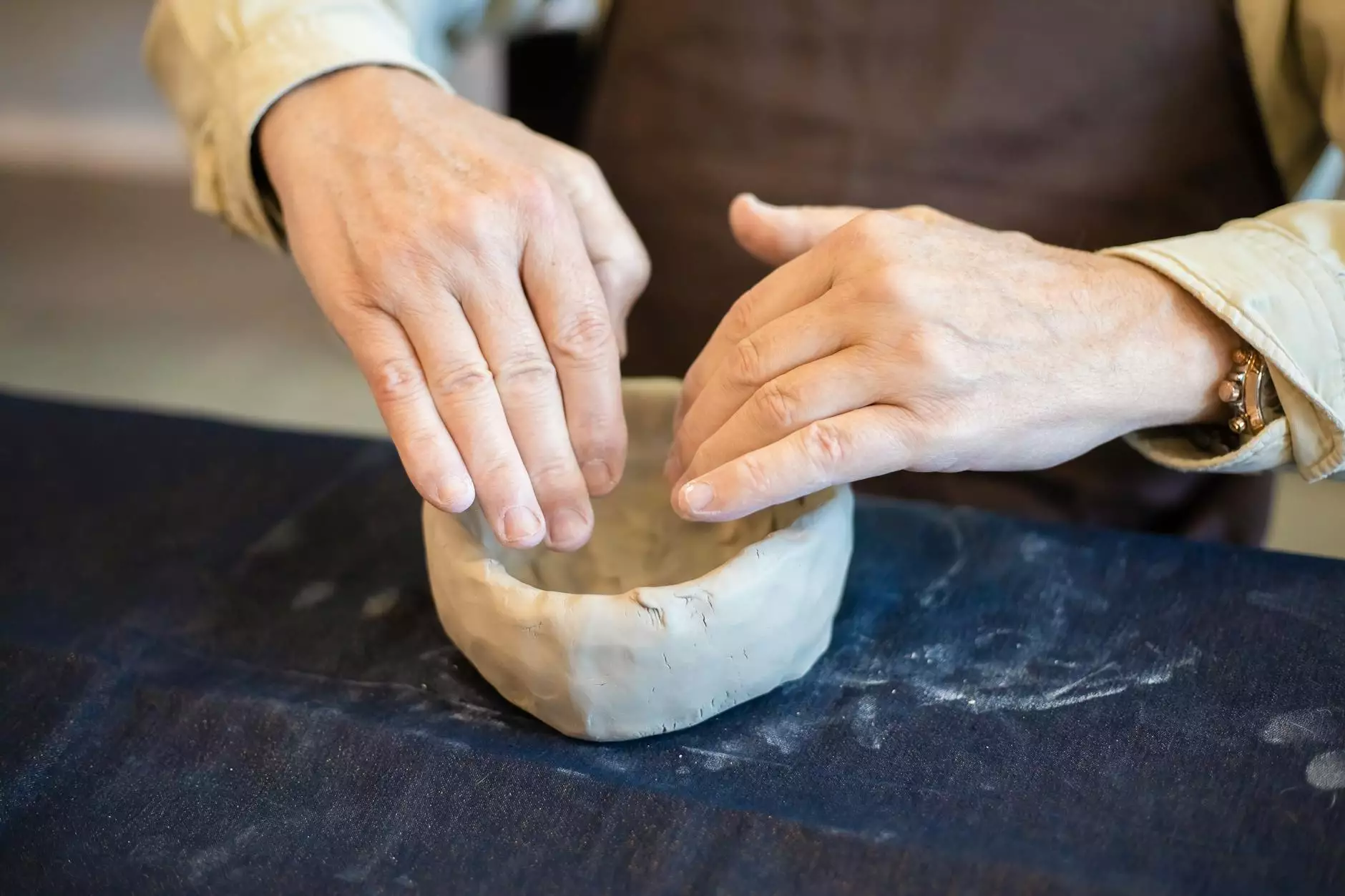
In the realm of advanced manufacturing, high pressure die cast tooling stands out as a cornerstone technology enabling the production of complex, high-precision metal components. For metal fabricators seeking to optimize their processes and deliver superior quality products, mastering this technique offers significant competitive advantages. With continuous innovation and meticulous engineering, companies like deepmould.net are transforming the possibilities of metal casting through cutting-edge high pressure die cast tooling.
Understanding High Pressure Die Cast Tooling: The Foundation of Precision Manufacturing
High pressure die casting (HPDC) involves the injection of molten metal into a precisely machined steel mold, or die, under high pressure. This high-pressure process guarantees dense, accurate, and intricate metal parts with excellent surface finishes. The die tooling used in this process is the critical component that defines the ultimate quality, consistency, and efficiency of production.
What is High Pressure Die Cast Tooling?
- Design Complexity: It includes the design and manufacture of dies capable of shaping complex geometries with tight tolerances.
- Material Composition: Typically constructed from hardened steel alloys to withstand extreme pressures and thermal stresses.
- Machining Precision: Incorporates advanced machining techniques such as CNC, EDM, and surface treatments for high dimensional accuracy and durability.
Advantages of Using High Pressure Die Cast Tooling in Metal Fabrication
Implementing high pressure die cast tooling presents several key benefits that cater directly to the needs of modern metal fabricators:
- High Volume Production: The durability and efficiency of the tooling allow for mass production with minimal wear and downtime.
- Exceptional Precision and Tolerance: Tight control over dimensions ensures consistent quality across thousands of parts.
- Complex Part Geometries: Enables the creation of intricate designs that are impossible to achieve with traditional casting methods.
- Superior Surface Finish: Results in smooth, ready-to-use surfaces, reducing or eliminating secondary machining processes.
- Cost Efficiency: Long-lasting dies and fast cycle times reduce the overall cost per part, increasing profitability for high-volume projects.
Design Considerations for Effective High Pressure Die Cast Tooling
Designing die tooling for high pressure die casting demands a meticulous approach to optimize performance and longevity. Metal fabricators must consider several critical aspects:
Material Selection
The choice of die materials influences the lifespan and thermal management of the tooling. Hardened steel such as H13, SKD61, or other premium alloys are favored for their balance of toughness, wear resistance, and thermal stability.
Cooling System Integration
Efficient cooling channels designed within the die help regulate temperature, minimize thermal stress, and improve cycle times, ultimately leading to higher productivity and better part quality.
Parting Line and Ejection System
Precise design of the parting line and ejection mechanisms facilitates seamless part extraction without damaging the die or the product, maintaining tight tolerances and surface finish.
Venting and Ejector Pin Placement
A well-planned venting system prevents air entrapment and casting defects, while strategic placement of ejector pins ensures smooth removal without distortions or damages.
Manufacturing High Pressure Die Cast Tooling: From Concept to Reality
The manufacturing process of high-pressure die cast tooling involves several sophisticated steps:
1. Conceptual Design & CAD Modeling
Using advanced CAD software, engineers create detailed models that account for part specifications, material flow, cooling, and ejection systems. This phase emphasizes simulation to predict potential issues like hot spots or ejector interference.
2. Prototype & Machining
Initial prototypes are crafted from the digital design, followed by high-precision machining processes including CNC milling, EDM (Electrical Discharge Machining), and wire-EDM to achieve exact dimensions and features.
3. Heat Treatment & Surface Finishing
The die undergoes heat treatment cycles to enhance hardness and toughness, along with surface treatments such as nitriding or coating to improve wear resistance and longevity.
4. Assembly & Testing
The components are assembled, and extensive testing, including trial runs and prototype casting, ensures that the tooling performs efficiently and meets all specifications.
Why deepmould.net Is Your Premier Partner in High Pressure Die Cast Tooling
As a leading name among metal fabricators, deepmould.net specializes in delivering custom high pressure die cast tooling solutions that encompass every stage of the manufacturing journey. Their expertise ensures that clients receive:
- Innovative Design Solutions: Leveraging years of experience to produce dies that maximize output and quality.
- High-Quality Materials and Precision Manufacturing: Using state-of-the-art machinery and durable materials for long-lasting tooling.
- Comprehensive Support: From design analysis to post-production maintenance, providing thorough guidance and support.
- Fast Turnaround Times: Prioritizing efficient project timelines to meet tight production schedules.
- Cost-Effective Solutions: Balancing quality and budget to deliver competitive pricing without compromising standards.
The Future of High Pressure Die Cast Tooling in Metal Fabrication
The evolution of high pressure die cast tooling is driven by ongoing technological advances, including:
- Automation & Smart Manufacturing: Integrating robotics and IoT for real-time monitoring, predictive maintenance, and reduced downtime.
- Advanced Materials: Developing die steels with enhanced thermal properties and wear resistance for extended tool life.
- Simulation & AI: Utilizing sophisticated software and artificial intelligence to optimize die design and process parameters before manufacturing.
- Sustainable Practices: Focusing on environmentally friendly processes, recycling materials, and reducing waste.
How to Choose the Right High Pressure Die Cast Tooling Partner
Success in high-pressure die casting depends heavily on selecting a reliable and experienced tooling partner. When evaluating potential vendors, consider the following:
- Technical Expertise: Proven experience in designing and manufacturing complex dies for your specific industry.
- Material Quality: Use of high-grade, durable steel alloys aligned with your production requirements.
- Customization Capabilities: Ability to tailor die designs for unique products and specifications.
- Turnaround Time: Commitment to meeting project deadlines without sacrificing quality.
- Customer Support & After-Sales Service: Providing ongoing maintenance, updates, and support solutions.
Conclusion: Elevate Your Metal Fabrication with Expert High Pressure Die Cast Tooling
In today’s competitive manufacturing environment, the strategic use of high pressure die cast tooling can dramatically improve product quality, reduce production costs, and accelerate time-to-market. Companies like deepmould.net exemplify excellence in providing comprehensive, innovative, and reliable die casting solutions tailored to the needs of metal fabricators. Embracing this technology means embracing efficiency, precision, and growth — essential for staying ahead in the dynamic landscape of modern manufacturing.
Investing in superior high pressure die cast tooling is not just a technological choice; it’s a strategic decision that empowers your business to produce high-quality parts consistently, meet increasing market demands, and achieve long-term success.